Industrial refrigeration systems predominantly use natural refrigerants, primarily ammonia and more recently CO2。能源效率和这些系统的有效操作是植物运营商的关键参数。
The focus of the white paper is the comparisons of hot gas defrost strategy control methods, both on the hot gas side as well as on the condensate drain.
This white paper is based on the article originally presented at 10th IIR Gustav Lorentzen Conference on Natural Refrigerants, Delft, the Netherlands, 2012.
Industrial refrigeration systems predominantly use natural refrigerants, primarily ammonia and more recently CO2。能源效率和这些系统的有效操作是植物运营商的关键参数。The focus of the article is the comparisons of hot gas defrost strategy control methods, both on the hot gas side as well as on the condensate drain. The key parameters analyzed on this paper are the efficiency as well as the speed of defrost, which is especially important for the productivity of the freezing plant.
作者建议机会改善热气除霜系统的控制。本文描述了氨系统的热气体除霜,表明了CO的特殊要求2plants where relevant.
Some of those requirements are derived from higher pressures and higher pressure differentials with CO2。该文章表明,当以最佳方式进行除霜时,可以节省多达植物能耗的5%,甚至可以节省更多。
This white paper is based on the article originally presented at 10th IIR Gustav Lorentzen Conference on Natural Refrigerants, Delft, The Netherlands, 2012.
就空气冷却者而言,解冻是“不可避免的邪恶”。霜需要融化,否则会严重影响空气冷却器的性能,并最终可以完全阻止空气流动。与热气体除霜有关的几种负面影响。需要额外的压缩能量来融化蒸发器鳍和管周围形成的霜/冰层。至少,该能量的一部分被转移回冷藏空间或加热蒸发器。最终需要在冷却过程中删除。最后,用于冷冻的时间不用于冷却。这可能是食品加工厂中的一个非常重要的因素,在食品加工厂中,解冻可以显着限制生产率水平。此外,其他重要但不太明显的后果可能会破坏诸如关键组成部分的机械应力之类的完整性。在阀门周围使用的阀门和控件上发现的许多故障可能归因于错误的阀门配置和 /或设置。
The main source of mechanical stress is the combination of high pressure coming from the condenser side, high discharge temperature and high pressure differential. When combined, those factors could be quite dangerous and even destructive. Today we also see that there is an increased number of companies using CO2for low temperature plants, and quite often in combination with hot gas defrost. At the same time, the situation with CO2in this case is even more complex than with ammonia, as the pressure level and pressure differentials are much higher. The complications of hot gas defrost with CO2可能导致某些客户避免这种解冻方法,并寻找其他替代方法,例如电气或盐水除霜。
热气体除霜是融化蒸发器上霜冻的最有效方法之一(Pearson,2006)。随着对减少能源消耗的关注,进行快速有效的除霜是实现制冷系统总体能源消耗目标的关键。在大多数情况下,与例如盐水除霜。本文重点介绍了可以应用于此类系统的阀门和控制配置以及优化过程的方法。
There are a few studies targeting the understanding and improvement of hot gas efficiency of refrigeration systems. A number of the critical points could be summarized as follows:
1. Hot gas defrost pressure. A popular misconception is that the higher the defrost temperature, the better. In reality a number of studies indicate (Stoecker, 1983) that a source of lower pressure and temperature gas could obtain good results as well. There is most likely an optimal pressure / temperature (Hoffenbecker, 2005) that would achieve the highest efficiency.
2.热气体除霜时间。在工业制冷中,基于安装启动期间调整的固定时间设置除霜非常典型。这种方法的问题在于,在许多情况下,这次将处于“安全的一面”,以确保拥有完全清洁的蒸发器。
当解冻较早完成时,实际上发生的事情是,解冻的效率显着下降。
3.在热气体除霜期间的另一个显着效率可能导致通过解冻压力调节器的蒸气。该蒸气需要重新压缩,并且还增加了对蒸发器的热气体进料的需求。蒸气传递的量取决于冷凝物线中除霜控制的类型。压力控制或液位控制。
4.在解冻过程中用于融化冰的能量量超过两倍(Stoeker,1983; Hoffenbecker,2005),实际上需要融化冰。其余的能量用于加热空间,蒸发器,管道和滴水盘。
5. Finally, it should be mentioned that the ice is first melted on the coil, then the ice crashes in to a drain pan and then finally melts completely.
这里重要的是该过程是顺序的。最初,线圈中对除霜的需求较高,并且仅在排水盘后期。
6. When the hot gas defrost is started, the initial refrigerant inrush might create a liquid hammer, especially if the evaporator still has some liquid refrigerant that has not been drained. This also occurs if the hot gas supply lines contains pockets of condensed liquid being propelled by the supplied hot gas pressure, and gas pockets to implode.
Let’s consider those issues in relation to the valves and controls used to control a hot gas defrost process.
图1给出了带有热气体除霜的典型工业制冷蒸发器。蒸发器的控制阀可以分为4个主要组:
1. Pumped liquid feed to the evaporator. This valve train typically includes stop valves, filter, a solenoid valve, a regulating valve, a check valve and a final stop valve.
2.热气体进料管线。传统上,它有一个停止阀,一个过滤器,另一个螺线管阀和一个停止阀
3. Condensate line. Here we either see a pressure controlled valve or a float principle to drain the liquid. Both significantly different defrost principles
as we see later.
4. Wet return line. This line needs to have an automatic shut off valve and a stop valve.
The defrost process could be divided into 4 main sections. First, the liquid supply to the evaporator is shut off. Evaporator fans should still run for sometime, suction valve remains open in order to make sure that remaining liquid refrigerant will boil out. Second, the suction valve will be closed, evaporator fans will be stopped, the hot gas solenoid valve will be opened and the feed of the evaporator with the hot gas starts. Thirdly, when the defrost is finished, the hot gas solenoid valve will be closed, the suction valve will be opened. Finally, the liquid feed is opened again, water droplets on the evaporator fins are allowed to freeze , and only then the evaporator fans will be started again.
Critical considerations in the hot gas defrost process are avoiding pressure/temperature stresses and system inefficiency by managing a slow pressure built up in the cooler at the start of defrost and at the same time a slow pressure release from the cooler after the process. Both hot gas solenoid and main suction valve selection are critical when aiming for a safe and efficient defrost process.
考虑到上述效率注意事项,让我们回顾传统的阀门配置。还应考虑与CO的解冻2is a more harsh one, and a conservative approach for CO2evaporators with hot gas defrost should be preferred.
Figure. 1 Typical configuration for an industrial refrigeration evaporator with hot gas defrost.
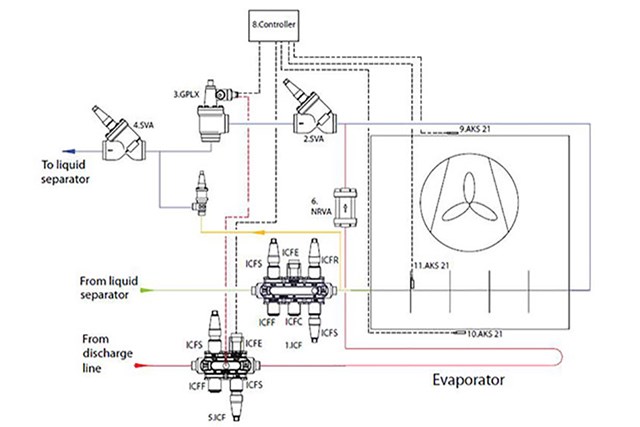
Liquid feed line has the minimal influence on the hot gas defrost process. What could be important to consider here, is the amount of liquid that is fed to the evaporator. In case PWM (pulse width modulation) strategy is used, the amount of liquid refrigerant in the evaporator will be lower. That should reduce the time needed to get rid of the liquid refrigerant. It could also be expected that the amount of ice is lower as well, as the temperature deviation on the surface in on/off periods is lower (figure 2).
This liquid feed strategy has been successfully used in a number of CO2systems with pumped recirculation. In ammonia systems, this control method has not been widely applied yet.
图2.脉冲宽度调制液体饲料
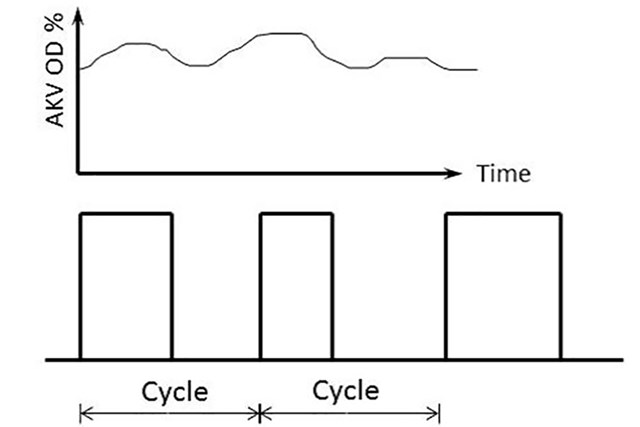
在蒸发器中喂热气的最常见方法是使用常规的螺线管阀。电动阀和电动球阀也已用于该目的,尤其是对于CO2systems. With higher pressures, and higher pressure differentials, the risk of liquid hammer in CO2热气体除霜系统比氨更高。显然,用电动阀的解决方案的缺点是它们设置更为复杂,并且带有电动阀的阀列比传统阀更昂贵。
Another point, which is especially critical for the ball valves, is that the opening speed must be adjusted to a relatively low level. A solution with 2 solenoid valves, the first sized for the required hot gas defrost capacity, and the second for 10-20% of the flow and installed in parallel to the first one (Figure 3) could be more cost effective and efficient. The smaller solenoid opens first and feeds the evaporator with hot gas for the first few minutes, increasing the pressure in the evaporator and supply lines in a controlled way. After that the second solenoid opens and the main defrost starts. This valve train configuration has already been used in a number of installations and in general proved to be successful.
电动阀在热气体除霜管线中的好处是,它们使得拥有智能热气控制成为可能。这可能不仅包括慢速开放,还包括缓慢(或调整后的)关闭。在这种情况下,当未根据时间安排而是基于其他参数(例如表面温度控制)进行解冻时,这可能是相关的。
最后,为了限制热气压 /除霜温度并最大程度地提高解冻效率;可以安装下游调节器。仅需要为连接到同一热气管线的一组蒸发器安装一个这样的调节器。阀的尺寸应使其可以为所有可能同时被解冻的蒸发器提供足够的热气体。
Figure 3. Hot gas feed line with double solenoid valve
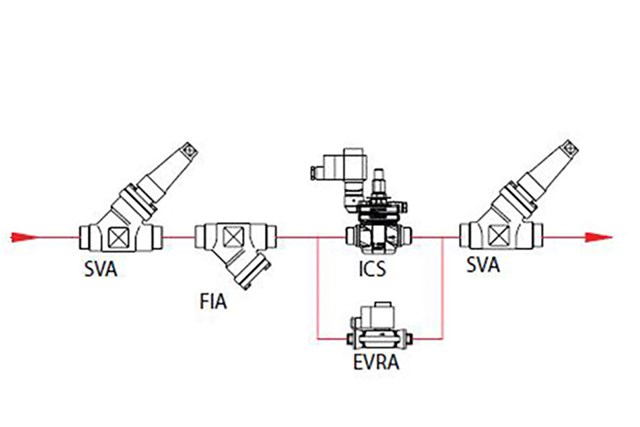
There is a wider variety in the regulation devices, used in condensate lines of evaporators with hot gas defrost. Differential pressure regulators are quite common, but upstream pressure regulators and float valves are applied as well. As discussed, the float valves are expected to be the most efficient controls for the hot gas defrost. A combination of float valve in condensate lines with downstream pressure regulators in hot gas lines would be a preferable one, in order to make sure that the defrost pressure is kept on the optimal level.
溶液中还有带有浮子阀的缺点。首先,成本可能相对较高。通过将浮子调节器安装在普通蒸发器冷凝线中的几个蒸发器中,可以部分降低成本。其次,对于高压制冷剂,例如CO2,浮动调节器很难找到。在这种情况下,必须探索替代方案。其中之一是来自其他行业的蒸汽陷阱,可以管理高压力。即使蒸汽陷阱越来越受欢迎,这些设备在制冷行业中并不是很常见。在本文中不会进一步讨论它们的细节,但是,所有有效的凝结物线中的浮子阀的考虑因素也应适用于蒸汽陷阱。
Figure 4. Float valves in condensing lines with multiple evaporators. Only valves in the condensing lines are indicated.
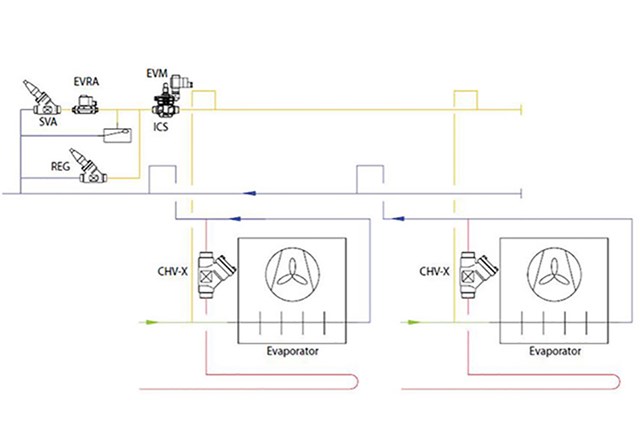
湿返回线中使用的控制阀是电磁阀,气体动力电磁阀(它们俩都需要具有旁路阀以避免解冻后的液体锤击),2步气电螺线管阀以及电动阀和电动球阀。首选的选项是2步气体电磁阀或电动阀。一方面,它们有助于避免使用液体锤,要么是由于2步功能,要么是由于打开速度缓慢。另一方面,它们在冷却周期中的压降最小,这在低温下尤其重要。
An advantage of the 2 step gas powered valves is that they require no additional settings. The second stage opens automatically when the pressure difference over the valve drops below certain value. Motorized valves require speed adjustment, but have no need for an additional hot gas line to power them. Motorized valves are especially popular for CO2系统,因为它们更容易获得更高的压力。带有旁路电磁阀的球阀也经常使用。溶液的好处是在冷却周期中的低压下降。但是,对茎的泄漏可能性是引起关注的原因。
In order to get an understanding of the efficiency improvement of the optimized defrost control against a conventional one, an example for the industrial refrigeration cold store has been calculated. The main parameters of the analysed coldstore are summarized in the table 1.
Table 1. Main coldstore data
Parameter | 价值 | 尺寸 |
Number of evaporators | 10 | |
Capacity of each evaporator | 100 | kW |
系统运行时间 | 50 | % |
Number of defrost of each evaporator, per week | 21 | |
蒸发/冷凝温度 | -35/30 | °C |
制冷剂 | R717 | |
系统警察 |
1.5 |
有关系统的解冻计算以2个步骤完成。首先,已经计算出融化冰和去除水的必要能量。计算以与Pearson(2006)相似的方式进行。假定鳍片之间的空气通道的阻塞为20%,而鳍间距为10 mm,导致1毫米冰的厚度。冰厚度是对解冻效率产生重大影响的参数之一。较高的霜冻厚度提高了解冻的效率,但对冷却过程中的效率产生负面影响。找到最佳的冰厚度是不超出本文的范围。
Table 2. Ice melting energy calculation
Parameter | 价值 | 尺寸 |
鳍间距 | 10.00 | 毫米 |
Ice Thickness | 1.00 | 毫米 |
Evaporator | 100 | kW |
重量 | 580 | kg |
霜密度 | 300 | kg/m3 |
表面积 | 450 | m2 |
霜冻重量 | 135.00 | kg |
Start temperature | -35 | °C |
末端温度 | 5 | °C |
比热冰 | 2.1 | KJ/kg*k |
比热水 | 4.2 | KJ/kg*k |
Specific melting heat | 336 | kj/kg |
Energy to heat the ice to 00C | 9,922.50 | kj |
Energy to melt the ice | 45,360.00 | kj |
Energy to heat up water to 50C | 2,835.00 | kj |
Total heat required to melt ice | 58.117.50 | kj |
The calculation was done for a standard industrial refrigeration evaporator from one of the major manufacturers. Energy losses during defrost are not included in to this calculation. According to Hoffenbecker (2005), the losses during defrost are on the level of 55% or more for lower defrost efficiencies. The losses depend on the defrost time and temperature, as well as on the frost thickness.
Assuming that for an optimized defrost process the losses are on the level indicated by Hoffenbecker (2005), as a second step of the defrost analysis let’s have a look at the comparison with a non-optimised evaporator. The main figures for this comparison are presented in table 3. Piping diagram for a standard system is presented on figure 1, and for an optimized on figure 5.
Table 3. Defrost efficiency comparison
计算基于许多假设,仅针对特定系统完成。但是,他们表明,不是最佳的热气体除霜不仅可以造成设备问题,还会导致功耗增加。表4列出了数据摘要,以及对未优化除霜的财务影响的评估。
表4.未优化除霜的额外费用
It is clear, that the more defrosts are needed, the higher the importance of the right valves configuration around the evaporator. If for some coldstores with weekly defrost the additional energy impact is minimal, for some freezing equipment with several defrosts daily an additional energy bill could be on the level of 5% or more of the energy consumption of the refrigeration equipment. And that is not considering the worst systems, with higher condensing temperatures to keep the defrost temperatures high.
上面的计算主要对氨系统有效。如果有CO2,应该使用其他除霜压缩机,这显然会改变能量平衡。与氨系统一样,不建议将主要压缩机的凝结压力增加。
图5.优化的除霜系统配置
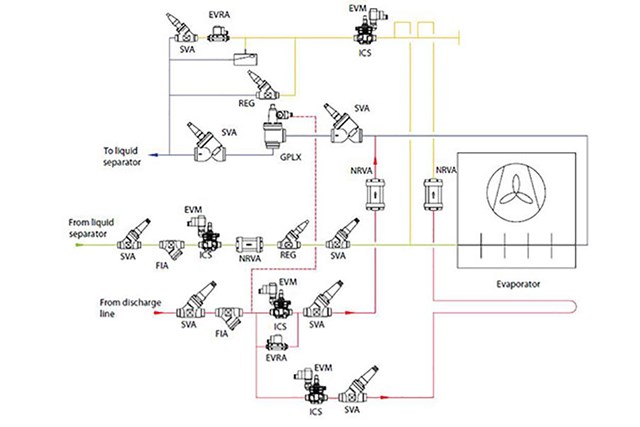
本文概述了热气体除霜系统的不同控制可能性。将当今可用的不同选项与做出的许多分析进行了比较,并指出了可取的选项。该分析的主要结论是,如果以最佳方式制定除霜,则可以实现系统的总能源节省5%或以上的系统总能源消耗。比较与当今使用的常见系统进行。如果以某些最坏的情况(但仍然不是很少)示例,则总体潜力看起来更大。
Further practical tests to confirm theoretical conclusions were started. However they were not finalized by the time the article was made and are subject to a further research.
Hoffenbecker N., Hot Gas Defrost Model Development and Validation, International Journal of Refrigeration, January 2005
Pearson A., Defrost Options For Carbon Dioxide Systems, 28th Annual IIAR Meeting, March 2006
Stoeker W.F., Energy Considerations in Hot-Gas Defrosting of Industrial Refrigeration Coils, ASHRAE 1983